- By Lanner
- In Customer Stories
- Posted 21/08/2018
Nissan Motor Manufacturing UK développe depuis plusieurs années des jumeaux numériques prédictifs pour améliorer l'efficacité de ses usines et optimiser sa prise de décision. Ce blog présente 5 exemples de la façon dont, à l'aide du logiciel de simulation prédictive de Lanner, WITNESS Horizon, des ingénieurs industriels ont créé des modèles pour répondre à des questions opérationnelles et stratégiques clés et pour faciliter le parcours de Nissan vers l'Industrie 4.0.
1. Atteindre de nouveaux objectifs de production de groupes motopropulseurs
Le défi : identifier les améliorations de processus nécessaires qui peuvent doubler les taux de production
Nissan se préparait à lancer un modèle mis à jour de sa voiture électrique Leaf, doté d'un nouveau moteur plus avancé. Pour répondre à la demande prévue des consommateurs, l'usine devait doubler le débit de production de son groupe motopropulseur, passant de 5 produits par heure à 10. L'équipe d'ingénierie industrielle souhaitait identifier les goulots d'étranglement potentiels avec une conception de production mise à jour, en se concentrant sur les améliorations de processus qui seraient nécessaires pour faciliter l'augmentation de production.
Le résultat : la prise de décision basée sur des faits aide à atteindre les objectifs
À l'aide d'une simulation prédictive, l'équipe a identifié un goulot d'étranglement crucial dans le processus de scellement. Une fois le joint mis sur le bloc moteur, il doit durcir pendant 15 minutes avant de pouvoir être testé contre les fuites. Même après avoir modélisé plusieurs scénarios de changement, ce blocage n'a toujours pas pu être éliminé.
Pour surmonter le problème, les ingénieurs ont utilisé le modèle pour expérimenter diverses contre-mesures. La solution consistait à mettre en place une autre boucle qui offre une capacité de stockage supplémentaire du groupe motopropulseur. Cela a augmenté le débit tout en fournissant le temps de durcissement requis avant le test d'étanchéité.
Nissan utilise maintenant ce modèle pour pousser l'analyse plus loin, en exécutant des scénarios qui permettent d'atteindre 15 tâches par heure et être prêt pour la future montée en puissance de la production.
Nissan Leaf en construction à Sunderland
2. Comprendre les taux d'échec des tests d'étanchéité
Le défi : réduire les risques de production pendant la phase de test d'étanchéité de la batterie
Un autre élément de la planification de la nouvelle Leaf consistait à analyser le processus de test d'étanchéité pour la batterie. L'équipe voulait connaître le taux d'échec maximal autorisé aux tests d'étanchéité qui permettrait tout de même d'atteindre les objectifs de performance.
Le résultat : des connaissances précises ont permis de répondre à la demande et d'atteindre les niveaux de performance
Le jumeau numérique prédictif a été utilisé pour modéliser des scénarios de production avec différents taux d'échec aux tests d'étanchéité. Il a permis de conclure que le taux d'échec ne pouvait pas dépasser 5,2 % sans affecter le débit. Cela a permis aux équipes d'ingénierie de planifier efficacement pour répondre à la demande.
3. Obtenir un processus d'usinage de culasse plus rentable
Le défi : minimiser les besoins en palettes sans affecter le débit
Dans le cadre de la fabrication des véhicules thermiques, les culasses subissent un processus d'usinage, de nettoyage puis une seconde passe d'usinage. Pendant une partie de ce temps, la tête est attachée à une palette. Les ingénieurs de Nissan prévoyaient de commander de nouvelles palettes mais étant donné le coût élevé de chaque palette, ils se sont demandé si l'installation pouvait fonctionner avec un nombre réduit sans affecter négativement les niveaux de production actuels.
La solution : 22 000 £ d'économies sur l'achat de palettes
Le jumeau numérique de la ligne d'usinage des culasses a été utilisé pour exécuter divers scénarios pour différents nombres de palettes, en analysant des facteurs tels que les intrants, le rythme de production et les volumes. Le modèle a montré que le stock minimum viable de 70 palettes serait nécessaire pour fonctionner à pleine capacité et avec peu de risque de goulots d'étranglement, nettement moins que les 100 prévues. Les avantages équivalaient à une économie globale de 22 000 £.
4. Réduction des goulots d'étranglement dans l'installation de peinture de pare-chocs
Le défi : déterminer le scénario de stockage optimal
L'installation de peinture de pare-chocs de l'usine de Sunderland reçoit des composants venant de 2 lignes de production, réussissant à traiter des pièces pour plusieurs modèles de voitures et une large gamme de couleurs de peinture. Des goulots d'étranglement commençaient à apparaître car l'installation manquait régulièrement d'espace de stockage. L'ingénierie voulait savoir combien de racks étaient nécessaires pour éviter d'avoir à arrêter la ligne de peinture.
Le résultat : une planification efficace à long terme qui maintient le débit
À l'aide d'un jumeau numérique de la ligne de peinture de pare-chocs, développé à l'aide du logiciel WITNESS Horizon, Nissan a créé un modèle visuel connecté au tableur de données de production. Le jumeau numérique prédictif a exécuté divers scénarios basés sur les différents modèles de voitures arrivant dans l'atelier de peinture et a déterminé le nombre optimal de racks de stockage pour garantir qu'aucune chaîne de production ne risque de s'arrêter. Le service de planification a maintenant fait évoluer le jumeau numérique pour tenir compte des nouveaux plans de lancement de véhicules afin que les exigences puissent être optimisées en permanence.
5. Analyser le dossier d'investissement pour une expansion
Le défi : Déterminer si l'installation devait investir dans une nouvelle station de film de protection pour la peinture
Un film protecteur de peinture est appliqué sur certains panneaux de voiture en fonction de la destination et de l'application, afin de protéger la finition et d'augmenter la durabilité. En préparation du lancement du nouveau modèle Infiniti, l'équipe d'ingénierie des garnitures et du châssis craignait qu'une nouvelle station de film de protection de peinture ne soit nécessaire pour répondre à la demande prévue.
Le résultat : 25 000 £ d'économies sur les dépenses d'investissement
Un jumeau numérique prédictif a été utilisé pour simuler le calendrier de contrôle de la production. L'équipe a exécuté des scénarios pour les exigences en matière de film protecteur de peinture et a déterminé que les installations existantes avaient une capacité suffisante pour faire face à l'augmentation prévue de la demande. Une solution pour faire face en utilisant l'équipement existant signifiait que les dépenses en capital dans une nouvelle station, qui auraient nécessité un investissement de 25 000 £, ont été évitées en toute confiance.
"Nous sommes un département assez léger et travailler avec Lanner et WITNESS nous a aidés à développer des modèles qui sont maintenant utilisés régulièrement pour prendre des décisions au sein de Nissan au Royaume-Uni. Grâce à la modélisation, nous avons pu mettre en œuvre des améliorations constantes dans nos processus, et la simulation est devenue un élément clé de l'adoption par Nissan de l'IoT Industriel et de la technologie intelligente. - Martin Perkins, ingénieur industriel, Nissan Motor Manufacturing UK
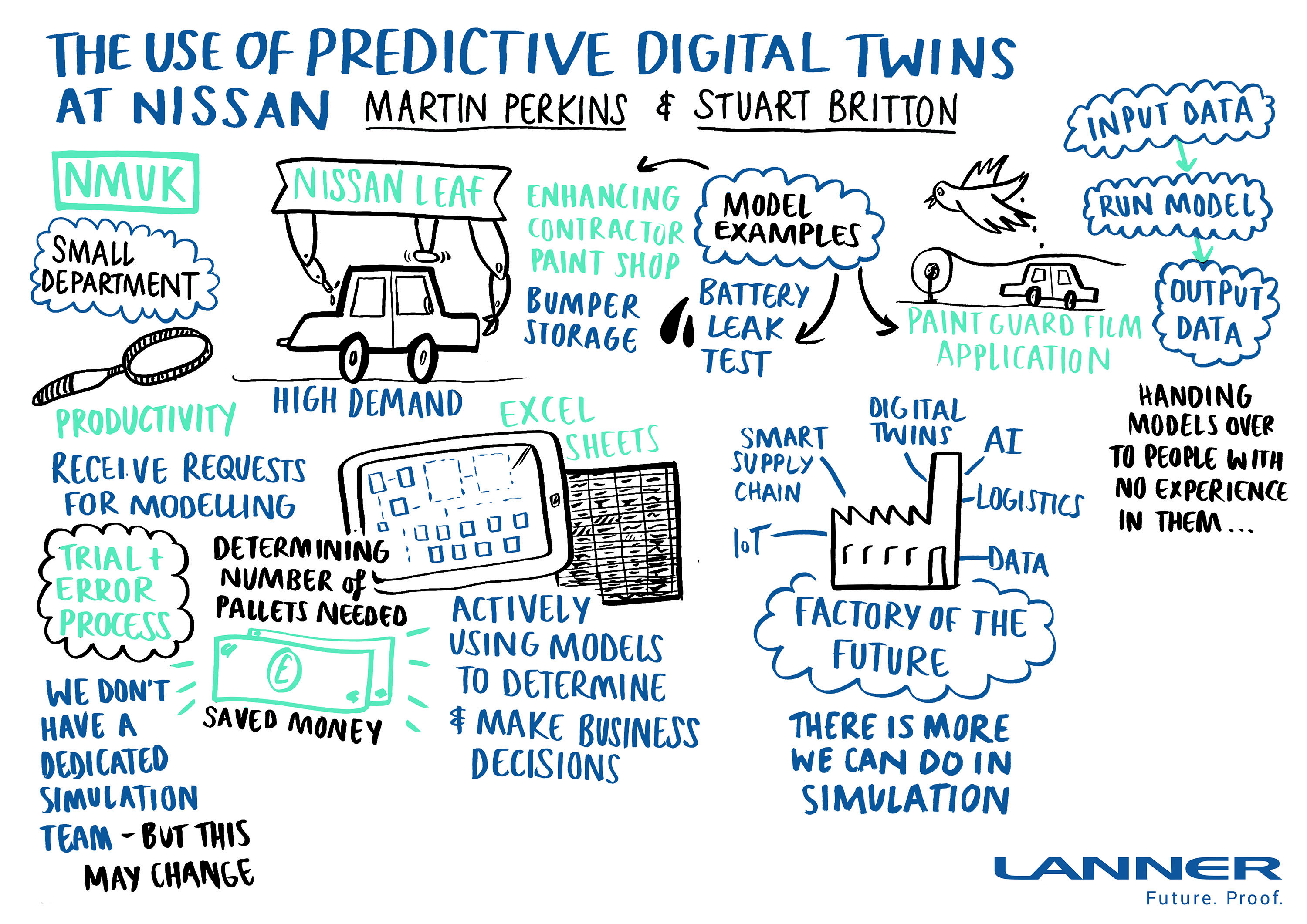