- By Ruby Hughes
- In Blog
- Posted 04/09/2018
When you hear the term “smart factory,” what comes to mind? If you’re an SME, it may involve leveraging robotics to boost automation, efficiency and throughput. If you’re a large aerospace OEM, it may involve autonomous AGVs, connectivity and real-time decision-making.
With the advent of Industry 4.0, the idea of the smart factory is bandied about regularly. However, there’s no one-size-fits-all approach to making your factory “smart”. And that’s why simulation and digital twins are crucial tools in the smart factory journey. These 4 steps demonstrate how you can leverage simulation to drive your business forward and maximise return on investment in new processes and tools.
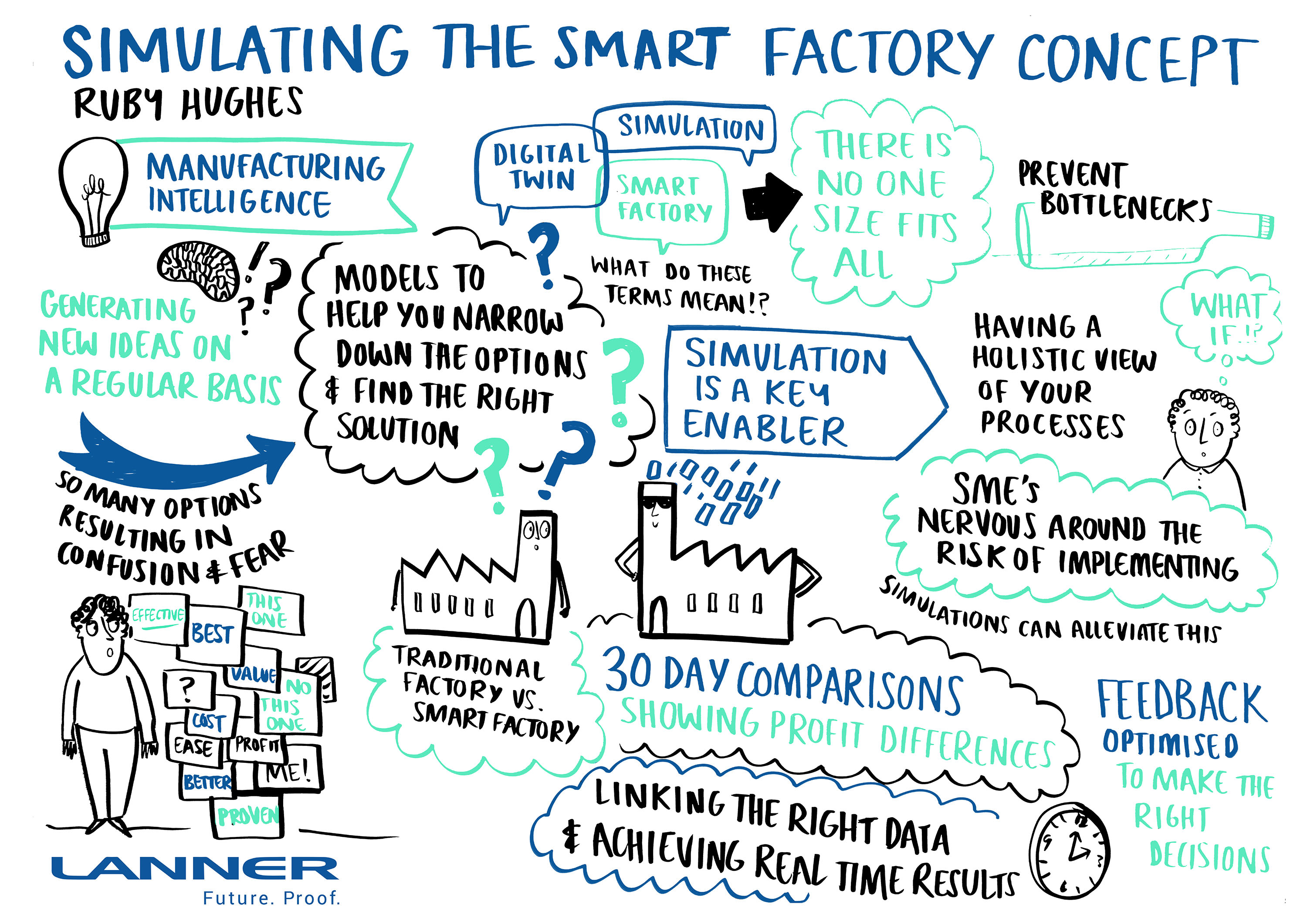
Step 1: Simulate
In order to become a smart factory, you have to start by understanding your current processes. Where are the bottlenecks? Do you need to improve the downstream processes, upstream ones or both? You need a clear picture of your starting point so you can identify weaknesses and take a strategic approach to introducing innovation.
Importantly, simulation doesn’t have to involve complex new systems. For companies starting out on the smart factory journey, Excel is best practice for data input - you can link it into systems like
Lanner’s WITNESS to drive the simulation. There are 2 reasons for this. First of all, everyone understands Excel, so it gives confidence that the right data is feeding into the model. Secondly, Excel makes it easy to tweak variables when you’re running ‘what-if’ scenarios in the simulation – you simply change the value in a cell, and the model updates accordingly.
Step 2: De-risk
Many sensors and entry-level Industry 4.0 technologies are low cost, so it can often feel like introducing them on the shop floor is a low-risk way to test the water. However, when you consider the combined cost of implementing technologies in an ad-hoc way – not to mention the opportunity cost of not taking the best approach – the risk quickly mounts.
The research backs this up. A recent study revealed that 60% of IoT projects have stalled at the proof-of-concept stage. That means more than half of initiatives have not been success stories.
Remember, the smart factory concept isn’t one size fits all, so you need to validate ideas for your context before implementing them. There are so many technologies associated with Factory 2050 and Industry 4.0 – from advanced automations and co-bots to vision systems and digital work instructions. Simulation demonstrates the KPI you would achieve if you implemented a specific solution in your factory.
Smart Factory Introduction - AMRC with Boeing from Lanner on Vimeo.
At the AMRC, we have a simulation demonstration for a battery pack assembly facility – a straightforward SME manufacturing environment. We start by simulating the current factory and fast forward for 30 days to get a baseline for production and profitability. Then we simulate production with a smart factory technology, again fast forwarding 30 days so we’re comparing apples to apples. Within 2 minutes, you can see the impact of investing in that technology within that specific production environment. With the technology, the model shows 2 times the throughput and double the profits – with less work on the input side. As a result, you can see the specific KPIs and easily calculate return on investment in the technology.
In other words, you’ve completely de-risked the decision to adopt that solution on the shop floor. And you have data that helps you benchmark and monitor the technology after implementation.
Step 3: Monitor
This brings us to the third step – monitoring. Research into monitoring is currently receiving a great deal of funding, and it’s a key area that’s constantly improving. The benefits are clear. Studies show that decision time for traditional factories is less than a month. For smart factories, it’s less than a second.
To reach that level of agility, you need connected systems and real-time monitoring. Compared to walking the shop floor, simulation gives you at-a-glance insight comparing the current situation to the benchmark. If you see that a robot has stopped, for instance, you can immediately see the onward effects.
The ultimate goal for smart factories is to use a series of digital twins that connect whole factories and supply chains in real time, giving you a holistic and powerful performance monitoring capability.
Step 4: Feedback
This fourth step doesn’t get as much attention as the other 3, but it’s critical to success. After all, there’s no point in simulating, investing and monitoring if you don’t feed the resulting decisions to the shop floor at the right time. You have to close the loop between insight and action.
Here’s an example of how this can work in a smart factory context. You get an alert that a machine is going to break down in 2 hours. AI technology and machine learning can then help analyse the issue and identify solutions for operators to review. You can run those solutions through the simulation to home in on the optimum one. System connectivity means you can feed the solution from the simulation into the PLC system. It can then be implemented through a combination of automation and manual input as required. You’ve closed the loop and eliminated the risk posed by machine breakdown – all within minutes.
Take an evidence-based approach to becoming a smart factory
The companies that succeed on this journey, whether they’re SMEs or global enterprises, follow these 4 steps.
Rather than experimenting with physical processes, assets and budget, simulation allows you to test changes in a risk-free environment – so you can make smarter choices to become a truly smart factory.
Ruby Hughes, Technical Fellow, Head of Manufacturing Intelligence Team, AMRC with Boeing
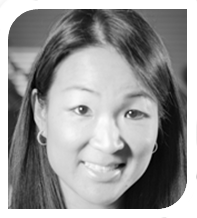